Beyond optimizing existing processes, 4IR, or the application of cyber-physical systems to industry, is an opportunity to reimagine the way manufacturing is done, trading in scale and scope for speed and modularity. A new tool in this space is microfactories: small, modular plants that offer a proximal, just-in-time option for manufacturing. Powered by data and other 4IR innovations, this new kind of facility bucks the economies of scale of more traditional factories, and embraces a small-scale, local solution to global supply chain challenges.
Some assembly required
Much like their more orthodox counterparts, microfactories optimize operations by leveraging technologies like data science, IoT sensors, and machine learning. Where they stand apart, though, is in their agility and modularity. Because of their smaller scale, facilities can be reconfigured rapidly, allowing them to swap between products or to open a new operations site overnight.
“Think huge 3D printing systems the size of a car, then plunk them in a room,” said Ben Wynne, CEO, and co-founder of Intrepid Automation. Intrepid is a San Diego-based startup developing industrial 3D print systems that power microfactories.
“Boom there’s your microfactory,” Wynne said.
3D printing is a compact, malleable technology that creates opportunities that wouldn’t exist otherwise. 3D printing is considered additive manufacturing, which when combined with the ability to reconfigure how and what it makes on the fly, makes it the quintessential technology in microfactories. Benefits like just-in-time manufacturing, more quality control, and the ability to swap out a few parts and produce a completely different product are game changers when trying to meet the complex challenges of a global supply chain.
“Because 3D printing is digital and distributed, you just need to send a file five days before parts are needed. We’ve started with medical devices and automotive parts, but the sky’s the limit,” Wynne said. “This technology allows for smaller batches, custom items, and delivers a faster, more efficient experience from order to delivery.”
Intrepid primarily builds enterprise-scale 3D printer systems for manufacturers. The company relies on data to disrupt the manufacturing industry, offering flexibility and modularity in a traditionally rigid space.
“It’s that pragmatism plus disruptive technology,” he said.
“It’s that pragmatism plus disruptive technology.”
Data in, data out
That disruptive technology is powered by data, while also producing valuable data itself. Wynne compares the data pipeline of a microfactory to that of fully autonomous vehicles.
“First step is to create a huge load of data,” he said. “As that data is being collected and mined, there is a rapid acceleration to fully autonomous vehicles. It’s the same for us: data is the key to minimizing variability from printer to printer, part to part.”
Nearly every aspect of a microfactory that Intrepid helps build, from machines to the finished product, is a data point collected and analyzed to improve the additive manufacturing process. No longer just machines, these IoT devices come with telemetry and metadata, learning and interacting with their spaces. While this data collection is prevalent throughout 4IR, microfactories are designed with this consideration from the ground up and leverage their smaller scale when building their data storage architecture.
“On the edge, we need to mine and query hot data very quickly, something only our flash storage can do,” Wynne said. “But you also need a long record of every part, machine, person, and movement that went into the creation of a part. That cold data is what helps us ensure quality from airplane parts to medicines.”
Every cycle, every day, every product, and every process produce data that are captured and can be analyzed in real-time. Temperature, for example, is closely monitored in these closed loops and can have a huge impact on the consistency and quality of manufactured goods. Operators can identify the problem and address it. Analyzing the data and changing something as small as an overheated component can prevent faulty products and save materials, time, and money, an ideal implementation of 4IR technologies.
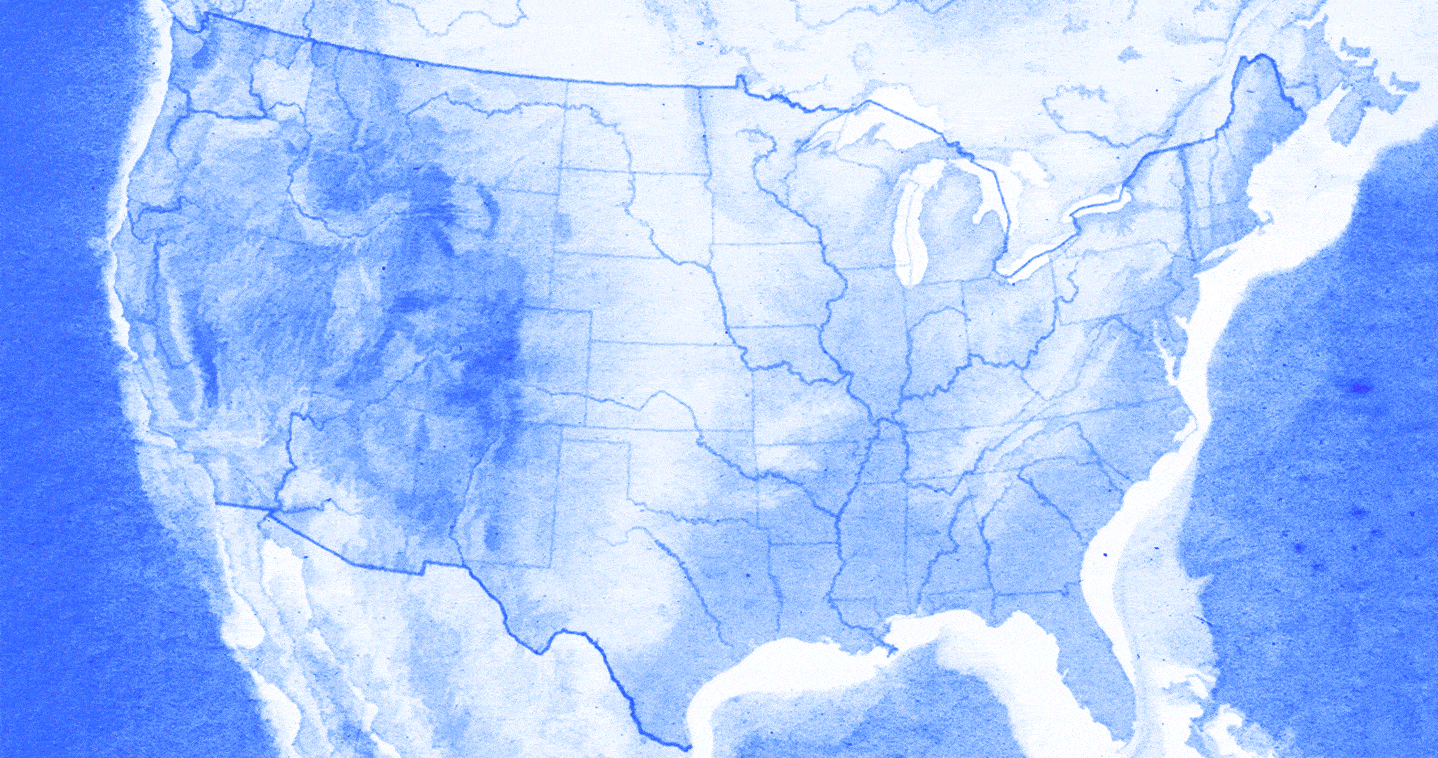
Microfactory, macro-impact
Microfactories enable dynamic and fluid logistics and manufacturing. The highly specialized machines of previous eras are replaced by more nimble and modular 3D printers, which don’t need to be housed in large-scale plants focused on economies of scale. This shift is driving interest and investment in distributed manufacturing, a system of manufacturing focused on smaller, dispersed manufacturing sites. Wynne sees microfactories and distributed manufacturing as a means to make supply chains more resilient.
“What if we could have immediately changed our supply chains around as soon we knew the [Suez] Canal was blocked?” asked Wynne. “Before when we worked with folks it was all about off-shoring, but now there’s a real hunger for our distributed, digital model.”
Beyond the supply chain, though, lies an opportunity to rethink manufacturing systems and infrastructure. Creating smaller manufacturing facilities around the world could help solve the last-mile problem. The could also create local jobs while making communities denser and more resilient. For Wynne, emergent challenges require bold solutions, and he thinks microfactories will help the industries of tomorrow tackle them with confidence.
“The time has never been better,” Wynne said. “This is the perfect time for us to reimagine what manufacturing could be.”