Innovation is rarely quick and often only obvious in hindsight.
Helium has been one of the greatest breakthroughs for high-capacity hard drives (HDDs). Being seven times lighter than air, helium creates less drag and turbulence when HDD platters spin. It runs at cooler temperatures, and when sealed, it keeps out humidity. All those benefits translate to dramatically increased data storage capacity, lower power draw, and better reliability.
Yet helium-sealed hard drives almost didn’t exist. It took several decades, and many impossible turns before a handful of engineers and scientists made a breakthrough that changed storage history.
Chasing the Holy Grail
Barry Stipe was a groundbreaking physicist at Cornell University when he was invited to do his post-doctorate at IBM in 1998. Two years later, he joined the company’s HDD research division and was tasked with cracking the code on helium-filled HDDs.
“I remember hearing stories about helium being the ‘holy grail’ for hard drives,” said Stipe. “Patent literature dates back to the 1970s,” he said, “but after decades of failure, most assumed practical helium HDDs were impossible.”
Helium is notoriously difficult to contain. Its atoms are some of the tiniest in the universe. They will zip through any pores or cracks in a seal, even atom-sized ones.
For hard drives, sealing helium wasn’t just about containing the gas. It was also about conforming to a strict form factor and existing manufacturing processes. Use expensive materials or reinvent the wheel, and the costs will quickly outweigh the benefits.
Mind the Gap
When Stipe began the project, a typical HDD had about 10 openings. Plugging those holes took all kinds of creative attempts — eccentric adhesives, metalized tapes, gaskets, polyamides, and even canning. Yes, the same technique the food industry uses for tuna.
Stipe had several grand failures of his own but then took a wildly different approach. He moved all the casing openings to the top, and rather than plugging holes, he created a thin metal foil as a second cover and began researching welding techniques used in other industries.
“As sealing the drive would be the very last step in the manufacturing process, I needed to make sure we didn’t damage any components by creating a lot of heat,” Stipe explained. But isn’t welding all about melting metal? He found the answer in satellite technology.
Space Exploration
Satellites use a welding technique leveraging lasers to hermetically seal microwave components. Unlike many other methods, the area affected by heat is very, very small.
Yet Stipe’s experiments failed on the HDD base casting. The aluminum alloy included just a little bit of copper, which would cause it to crack. So, he looked again to the aerospace industry to find an alternative alloy that wouldn’t pop, crack or sputter under the heat.
Once he solved that, there was just one challenge left: finding a way to get electricity and data in and out of the drive without breaking the seal. This time his inspiration came from a more familiar and faintly less glamorous object: refrigerators.
“Until then, I didn’t quite appreciate how good of a seal was needed to contain Freon in refrigerators. The refrigerator industry used glass-metal feedthroughs that were also low cost and produced by the millions,” Stipe said.
But nothing was straightforward on Stipe’s quest. Soldering steel feedthroughs to the oxide layer of the HDD casing proved impossible. He had to conjure up a mask that would make the solder stick, and nickel transpired as the ideal plating element.
After hundreds of testing hours, Stipe could prove a reliable, low-cost, and form factor-abiding way to seal helium in HDDs for 100 years. It was brilliant in its simplicity but at a satellite’s distance from being manufacturable.
The Quest Goes Global
By then, it was 2003, and IBM’s HDD division was sold to Hitachi Ltd. Akihiko Aoyagi, an ambitious mechanical engineer, was ending a two-year assignee post in IBM’s Almaden Research Center right as Stipe’s findings moved from research to technology development.
Aoyagi was intrigued by the project and as chance would have it, when he returned to Japan, he was asked to lead the engineering team developing a commercial helium-sealed HDD, a worldwide project based on Stipe’s research.
Technical challenges mounted from the get-go. Stipe’s alloy was too gummy for the supplier’s machines, and the existing alloy created sealing mayhem. Tiny pockets of gas and moisture got trapped in the aluminum during the die-cast process. When the laser would heat those pockets, they would explode, sending helium on its way up.
“This was an almost impossible project,” Aoyagi said, “I knew no one would blame me if we failed, so I thought ‘I better enjoy trying.’”
Two years later, the research team had promising results. They found that with a particular shifting of the laser and a silicon-rich alloy, they could control the explosion’s angle in a way that it doesn’t scathe the seal. Only seemingly effortless, this “edge welding” technique was novel, patent-worthy, and earned the team an award from the Japan Institute of Invention and Innovation.
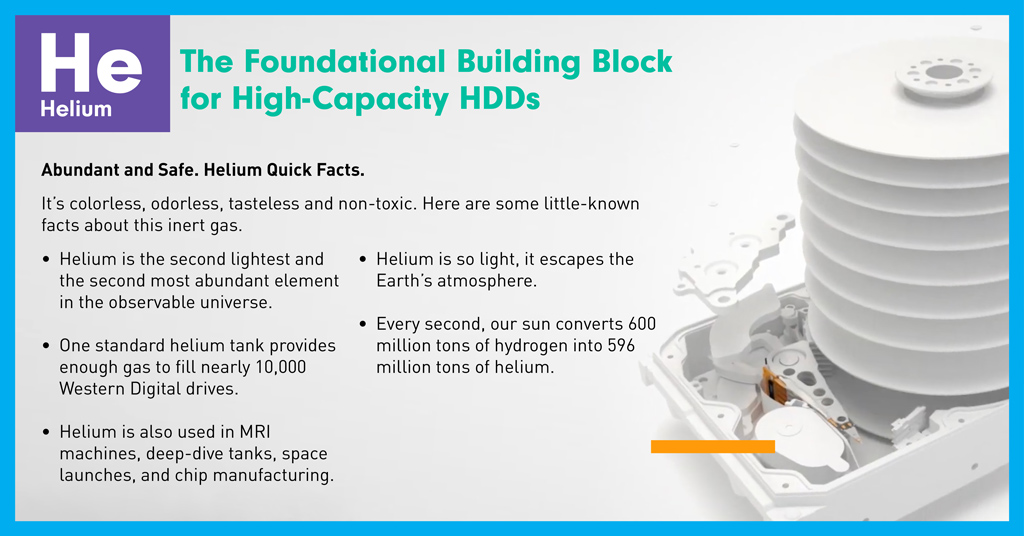
Sealing Fate
Despite the team’s success, the project was terminated. “The manufacturing investment was deemed too high, and there were alternative ways to increase HDD capacity,” said Aoyagi. The entire team was dismissed but Aoyagi was resolute about the technology and he got permission to continue as the project’s sole engineer.
Around that time, “big data” and cloud computing took off in every industry. For the first time in history, more objects were connected to the Internet than people. Demand for high-capacity HDDs increased greatly, and it was clear they would be critical in the world’s data-hungry future.
The project resumed in 2009. It took just half a year to create an unprecedented 7-platter HDD prototype, but another four years to solve the plethora of manufacturing process challenges. It’s one thing to produce an effective seal in a pilot program, but a whole other challenge to produce a reliable product with a near 100% manufacturing yield.
Sealing the Deal
In 2013, after Western Digital acquired Hitachi Global Storage Technologies, the company shipped the world’s first commercial helium hard drive. It had 50% more capacity than any air-filled hard drive, and consumed only three-fourths the energy. It was radical. It was revolutionary. And it was already testing with customers like Netflix, CERN, and the leading names in social media and search.
It took a little over a year to ship the first million drives. Two years later, ten million drives were shipped. Today, Western Digital ships about a million helium-sealed drives every month.
Helium HDDs became a foundational technology for storing the world’s data. It took no less than groundbreaking science, hard-won innovation, and a dash of the impossible.
– – –
More on Helium-Sealed HDDs:
Western Digital’s HelioSeal® platform.
Why helium HDDs were pivotal in creating the first-ever black hole image.