Accelerating manufacture and delivery of personalized PCs to global customers
For businesses around the world, supply chain resilience has never been more important. To keep production lines running smoothly, it’s crucial for enterprises to plan effectively and react quickly—from production planning and scheduling onwards.
This article explains, step by step, how Lenovo optimized its own supply chain through the implementation of AI-powered Advanced Production Scheduling (APS) capabilities that we developed in-house. The results have been dramatic: 24% more production line capacity, 19% higher production volumes, a 3.5X increase in on-time deliveries, and the acceleration of production schedule planning from two hours to two minutes.
The challenges that we faced in our global business are by no means unique. The Lenovo APS solution could deliver similar transformative benefits for manufacturing and logistics companies of practically any type.
Time is of the essence
As the world’s #1 PC manufacturer by annual number of units shipped, Lenovo understands the challenges of orchestrating long and complex supply chains. To precisely tailor its products, Lenovo sources more than 300,000 different materials from 2,000 international suppliers.
Lenovo’s flexible manufacturing systems allow it to produce several devices on one production line. However, every time a team retools to create another product, they need to pause the line. So, it’s critical to keep production line changes to a minimum without delaying production for urgent orders.
Previously, teams relied on spreadsheets to manage production schedule logic, but the growing number of customized solutions dramatically increased the number of variables—the situation became simply too complex for a human to handle.
Innovating with AI
As part of a wider smart manufacturing transformation, Lenovo set out to find a new approach to production scheduling. The aim was to implement APS capabilities—empowering planners to harness AI and big data analytics to streamline production lines and maximize throughput.
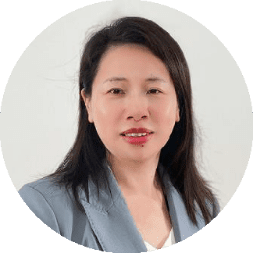
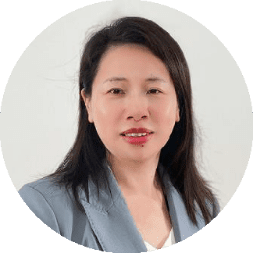
Bai Zhizhi, Order Management Senior Manager at Lenovo, explains: “To make our vision for APS a reality, we looked for a way to rapidly process large volumes of data in an intelligent, automated way. We evaluated the leading APS solutions on the market, but none of them met our demanding operational and technical requirements. We needed to find another approach.”
Lenovo powers Lenovo
No existing APS solutions on the market were able to handle the sheer scale and complexity of Lenovo’s production scheduling operations. So, Lenovo decided to build the solution in-house—a first-of-its-kind project for the company.
The Lenovo project team collaborated with stakeholders across the company to build the new planning system. Using a digital twin of one of its key manufacturing facilities, the team ran repeated simulations to optimize the planning logic based on real-world data.
Creating a self-learning solution
The Lenovo team leveraged AI and machine learning technologies to coordinate and prioritize multiple scheduling variables in real time, including thousands of employee schedules and hundreds of thousands of components.
The team invested significant time in mapping out and optimizing the new scheduling processes. Over many iterations, Lenovo refined the planning logic for the new system and identified more than 40 integration points with upstream and downstream systems.
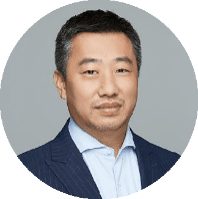
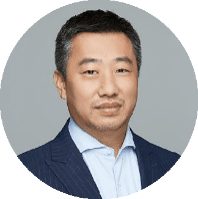
Built on emerging technologies such as sequential planning algorithms based on deep reinforcement learning, Lenovo’s new AI solution continuously
learns and adapts every time it creates a production schedule. As a result, the solution becomes more and more effective over time.
Rapid development
By building the APS solution in-house, Lenovo ensured that the new platform met its demanding requirements for production scheduling—and all in record time.
Haiming Gan, Senior IT Manager, Digital Insight at Lenovo, comments: “With a lean team of 10 internal experts, we developed a leading-edge APS solution in just six months. The AI solution is delivering excellent results against several key performance indicators, and we’re anticipating further benefits as we continue the rollout.”
The modular architecture of the APS solution means that it can be configured to meet the requirements of practically any type of manufacturing—and Lenovo has already demonstrated the solution to representatives from several different companies.
Deploying worldwide
Lenovo is now rolling out its AI-powered planning solution to its global manufacturing facilities. The APS solution runs on a central global platform and is delivered via a software-as-a-service (SaaS) model—enabling the company to deploy new instances rapidly and cost-effectively.
Today, more than 20 Lenovo facilities are leveraging AI-powered insights from the APS solution. Planners can analyze scheduling factors automatically, eliminating the need for time-consuming data collation.
Lenovo has slashed the time taken to create production schedules from two hours to just two minutes. Over 75% of the process is now automated, and the new solution has an adoption rate of almost 95%—a testament to how well it meets the needs of the company’s planners.
Minimal delays, maximum customer satisfaction
Thanks to the power of AI, Lenovo can generate ultra-efficient production schedules faster than ever. As a result, the company is boosting manufacturing throughput, enabling it to accommodate growing demand for customized products.
In fact, the company has unlocked 24% more production line capacity, allowing it to lift production volumes by 19%. And even though the number of complex and customized orders is growing, Lenovo has boosted the number of on-time deliveries by a factor of 3.5, helping the company to delight its customers.
Zhizhi concludes: “Looking ahead, our goal is to expand the APS solution worldwide, maximizing all available production capacity and supporting Lenovo’s ongoing smart manufacturing transformation.”